See This Report on Sheroz Earthworks
See This Report on Sheroz Earthworks
Blog Article
What Does Sheroz Earthworks Do?
Table of ContentsThe Buzz on Sheroz EarthworksThe Best Strategy To Use For Sheroz EarthworksThe Basic Principles Of Sheroz Earthworks The 8-Minute Rule for Sheroz EarthworksThe Best Guide To Sheroz Earthworks
When contractors like Rasch Construction execute a quality control system for their dozers, it helps them make fewer errors when grading. This system continually monitors the blade, makes little changes to the placement of the dozer blade during grading and decreases rework. If the dozer does not grade the ground specifically as intended, the operator can realign the dozer blade to fix minor blunders and make exact changes to reach the wanted quality.When thinking about the purchase of a grade control system for a dozer, drivers will need training on how to use the system. New drivers and experienced veterans must be acquainted with the elements of the 3D grade control system, including the equipment (for example, the sensing units and receivers) and the software program components.
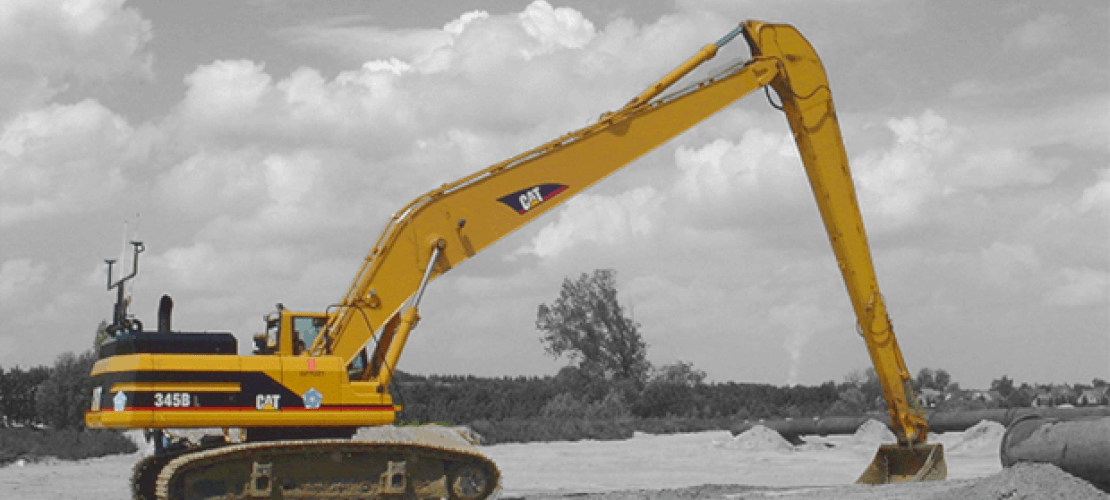
The Best Strategy To Use For Sheroz Earthworks
This includes grade information, altitude data and various other relevant metrics presented on the LCD screen inside the dozer's cab. Last, operator training need to consist of how to effectively control the dozer blade making use of the 3D quality control system. This assists them understand just how the system adjusts the blade in action to quality variants.
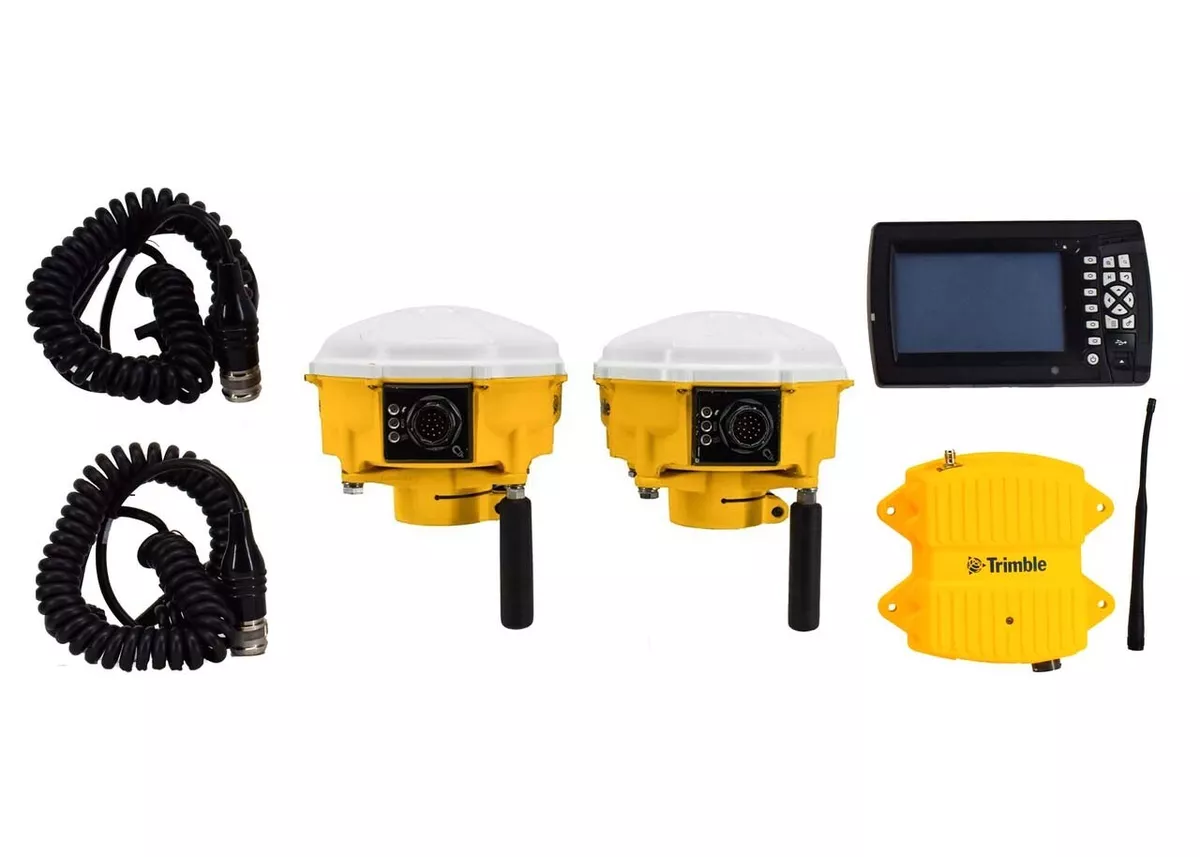
Product savings: If the quality is much more exact, a professional may need less product for the jobsite. Operators may likewise minimize the requirement for rework and enhance expense financial savings due to labor and products - https://www.twitch.tv/sherozau/about. To find out more about exactly how to enhance jobsite efficiency with grade control innovation, explore the offerings from Trimble and comparable firms
Advice and precision control, the base components of modern-day maker control for building and construction, have continued to develop given that wide productization started in the mid-1990s. However, the value recommendation has actually become even sweeter because, with worth being realized beyond the return on investment (ROI) of the general specialists and the total task cost for the clients.
Sheroz Earthworks - The Facts
The roots of machine control stretch back a century. The Historical Building Devices Association (HCEA) posits that the A.W. French & Co. "energy grader" of the 1920s, a crawler-mounted unit that used stringline control, may be the very first instance and this before electronic devices and computing. It was the advent of real-time kinematics (RTK) for GPS in the mid-1990s that brought maker control as we understand it to the construction site, and coincidentally to accuracy farming.
After that it transferred to accuracy control, such as blade control, and later on propagated to more classes of mechanized devices, boosted with additional sensor combination. The effect on construction and farming has actually been indisputable: performance gains, much less rework, much more effective handling of materials, much shorter timelines, site safety and security improvements, and a lot more - https://youmagine.com/sherozau. These advantages are as apparent to customers and drivers as they were in the early days of fostering, gains from nearly three years of technology
Automation is not simply about speed; it is likewise about much better control of the tons and stress on the equipment and relocating simply the appropriate amount of products so as not to put a concern on it. (Image: CHCNAV) These two activities, as each of our spoken with experts testify, represent the lion's share of recognized productivity gains.
The Basic Principles Of Sheroz Earthworks
"In addition to the skid guide systems, there are more excavators produced than all the other devices types incorporated," said Daniel Sass, product supervisor of machine control at Hemisphere GNSS. "Excavators are the workhorse. And people use them differently, and they utilize various other items of equipment to complement excavators somewhat in different Get More Information ways.
Absolutely, by quantity it is excavators and portable excavators." Numbers help tell the story. "In the United States, at least in a three-year period from 2019 to 2022, regarding 253,000 excavators were marketed, for which I have quite dependable data, yet only 61,000 dozers and only 7,000 scrapes," Sass stated
If you go to Europe, where they make use of excavators for lots of various other tasks, the proportional impact may be higher." Operators can easily evaluate the ROI of going electronic for individual pieces of devices such as excavators, yet part of the incentive might be that general contractors are needing subcontractors to be outfitted and prepared to match a more complete digital website.
"A whole lot of larger websites. "Just how do you move the product? With driver support, Clark stated, it is not uncommon to see productivity gains of 30% to 40%, even with unskilled operators.
The Facts About Sheroz Earthworks Revealed
There are substantial gains to be made in driver aid for much less complicated heavy tools, such as compactors. "Commonly a contactor will certainly place a much less experienced driver in the compactor," Clark said. "In manual days, to overcome the capacity of under-compaction and missing out on spots, they would certainly develop quite a huge overlap, perhaps up to 40% of overlap between paths.
Report this page